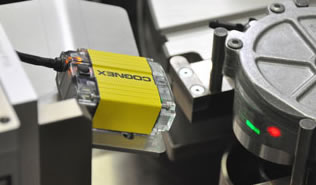
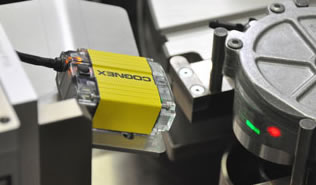
-1、提高生產作業效率 1.1、減少大部分生產線及倉庫手工記錄工作,節約人工和紙張。 1.2、減少管理工作人員往返產線、倉庫、辦公室的次數。 1.3、協同工作,實際各部門之間的數據銜接,減少因書寫或轉達錯誤造成的數據混亂,提高管理精度。2、實際生產數據實時體現 2.1、各業務流程與BTS共同制定數據標準,實現系統之間協同工作,數據無縫連接。3、數據可追溯性 3.1、通過采用一維碼能物料、生產線別、膠盆號、托盤編號進行標識,實現條碼數據綁定實物對象。 3.2、經過生產、再加工、出庫、入庫后的數據都綁定到一個膠盆條碼上,實現數據轉移有查詢依據。 3.3、通過數據庫記錄每個生產環節,實現可從成品追溯到物料,或從物料追溯到成品。4、減少倉庫出錯貨,提升庫存準確性至99%以上 4.1、出庫流程更快速,只需要用掃描器掃描,無需太多人工判斷,當出現錯誤后手持終端將自動警示音與震動警報,實現快速出庫。 4.2、通過先進先出管理模式,減少積壓舊庫存。 4.3、歷史數據無需人工統計,自動匯總;數據實時,準確。 4.4、為追溯查詢提供重要數據。5、提供實時數據信息 5.1、可實時監控生產作業過程,減少現場管理難度。 5.2、提高員工管理水平,隨時獲取所需的統計報表。 5.3、更好的控制工作量。 5.4、為將來的改進和管理提供更好的效率控制。
生產流程
追蹤要求
產品上有一個3個字符組成的代碼,要求從該代碼可以追蹤各個原材料的批次、注塑機號、日期、注塑模號、噴油日期、油漆批次、組裝日期、WRIN NUMBER、卡通箱號段等, 亦可以逆向追溯。
追蹤部件
成品可接觸的所有物料; 不含膠袋,INSERT紙箱等包裝物料;
其它特別指定的原料或部件(如果需要的話)。
條碼追蹤設想
在物料周轉膠盆上加一張固定的BARCODE,流通到不同的工序時掃描膠盆BARCODE記錄物料的流向;
發料時系統自動識別是否為最早的批次,如果不是先入先出系統會提醒;
系統自動形成追蹤文件;
系統可以查物料的數量,配件數量以及成品數量信息等。
系統建設要求/理念:
配件的發放:需遵循先入先出的原則;
槍: (工廠建議)盡量減少掃描槍的數量(和使用的人數);
資料和數據的輸入:
不確定且沒有規律的信息考慮人工輸入,如物料批號
不確定但有規則的信息考慮系統默認但可更改,例如日期、班次等
錄入量少的信息考慮人工輸入,例如產品D/C、WRING NUMBER,成品箱號等
其它與產品相關且不變的信息從《產品基礎資料》中自動獲取,例如產品/配件編號、名稱、膠料名稱、色粉編號、油漆編號/名稱,每盆數量等
周轉膠盆
每個(組)膠盆上有一張手寫的貼紙,包含一些簡單的信息用于目視管理,例如配件名稱,數量,生產日期,機號等
在物料周轉膠盆上加一張固定的BARCODE,流通到不同的工序時掃描膠盆BARCODE記錄物料的流向;
每個卡板上有一張條碼,根據需要可以將卡板上的所有膠盆條碼和卡板條碼關聯。
啤機編號及班次
將每臺啤機編號并生成固定條碼
將班次形成固定的條碼
(噴油線,也可定義每個產線的固定條碼,方便與膠盆數據綁定)
產品基礎資料
開產前,編寫產品的基礎資料文件,與系統聯網,關聯信息可自動獲取;周轉盆中部件的數量可以開產后再加入系統的《產品基礎資料》中。
減少生產過程中的反復輸入以及減少人工錄入錯誤。
本系統由三大部份結成:1、條碼追溯軟件系統(Barcode Traceability System,簡稱BTS),2、硬件設備、3、無線網絡;
BTS軟件系統分為以下幾個功能模塊:
主要模塊包括系統及用戶管理,基礎數據管理,生產掃描業務(啤機生產定義,噴油生產線定義,移印生產線定義,裝配生產線定義,委外加工定義),原料,半成品,成品入庫、出庫,倉庫管理,生產數據查詢,物料追溯查詢,查詢統計報表等。
物料標簽要求:
條碼貼紙規格:60mm(高)*100mm(寬)
膠盆標簽要求:
條碼貼紙規格:30mm(高)*50mm(寬)
Barcode_Container_100001
托盤標簽要求:Barcode_Pallete
條碼貼紙規格:30mm(高)*50mm(寬)
Barcode_Pallete_10001
生產流程圖
生產流程一般歸類為以下幾個流程
1:原料入庫【如膠料、色粉入庫】
2:原料出庫【如膠料、色粉入庫】
3:生產半成品【如啤件(白件)】
4:半成品入庫【如啤件(白件)、啤件(不需要再噴油件)入庫】
5:半成品出庫【如啤件(白件)、啤件(不需要再噴油件)出庫】
6:半產成品再加工【如白件進行噴油 / 移印】【與第3部操作一致】
7:(再加工的)半成品入庫【如:噴油件 / 移印件入庫】【與第4步操作一致】
8:(再加工的)半成品出庫【與第5步操作一致】
9:半成品組裝【如噴油件(或不需要噴油膠件)、外購件組裝后的產成品】
10:成品入庫
11:成品出庫
1、生產線生產定義【(A:啤機生產線定義)(B:噴油生產線定義)】
每臺單色啤機對應一個模具,雙色啤機對應兩個模具,并生產一個產品中的某個部件;
(每條噴油生產線對應生產一個部件)
1.1:每個班次生產前,負責人先檢查并核對啤機生產相關信息(使用掃描器掃描啤機條碼,顯示啤機號,模具號,生產產品對象,采用的膠料,色粉,當前班次等信息);
(如果為噴油線:掃描產品部件條碼,錄入該部件對應的每個顏色的批號,班次等信息)
1.2:負責人可修改內容有:模具編號(自動對應生產產品),膠料批次號,色粉批次號,班次號;
(如果為噴油線:可修改油漆的批次)
1.3:1個班次的生產,可能采用不同批次的物料,負責人可增加多個批次號的膠料、色粉;
(如果為噴油線:可增加油漆的批次)
(下圖為噴油批次對應圖)
2.1:生產入庫時,使用手持終端掃描啤機編號,自動顯示模具編號,膠料名稱及批號,色粉編號及批號, 班次,產品信息,產品對應的部件信息;(當白色啤件經過噴油后,再入庫時,同樣掃描噴油產線編號條碼,獲取生產對象信息,采用油漆批次信息,班次信息等)
2.2:確認無誤后,掃描產品部件條碼(預先打印好的產品部件條碼對應表);
2.3:第一次掃描膠盆條碼前,系統將提示是否需要與托盤關聯,如果確認需要,將先掃描托盤條碼,托盤條碼只掃描一次,接下來只需要掃描膠盆的條碼,系統將將自動關聯托盤條碼與膠盆條碼;
2.4:換另外一個托盤時,選擇更換托盤條碼,并掃描新的托盤條碼即可;
2.5:生產與倉庫交接后,倉庫人員掃描托盤條碼,將提示貨物應存放位置,選擇或掃描一個庫位,確認該貨物擺放在到個位置;
膠件出庫包括:啤件(白件)出庫,啤件(不需要再噴油的膠件)出庫,經過噴油后的膠件出庫;
3.1:掃描膠盆條碼,(不是選進選出的膠盆條碼進行提示或警告);
3.2:將膠盆條碼與噴油產線綁定(系統將判斷該產線準備生產的部件信息與膠盆存放的部件信息是否一致,不符合的進行警告);
3.3:經過確認后,該膠盆里的所有歷史與該產線進行綁定,同時綁定新的油漆批次信息(生產前,生產負責人進行了批次賦值,為下一步裝入新膠盆條碼做數據綁定)。
產品組裝模式:由自制半成品、外購件進行組裝成成品。
4.1:生產前,生產負責人對組裝線別進行生產設置,包括生產產品對象,生產日期(D/C),卡通箱號段,Wrin Number等 信息;
4.2:掃描所有膠盆條碼(啤件,噴油件),再掃描組裝線別條碼,數據進行綁定;
4.3:掃描所有外購件批次條碼,再掃描組裝線別條碼,數據進行綁定;
4.3:完成所有數據綁定過程。
5.1:因膠盆破裂或需要更換,需要將數據進行轉移;
5.2:選擇膠盆數據替換功能,掃描舊膠盆條碼,再掃描新膠盆條碼,確認替換;
6.1:物料查詢:掃描物料條碼,顯示物料編號,物料名稱,供應商,批次號等信息;
6.2:產線數據查詢:掃描產線條碼(啤機編號,噴油線編號,組裝線編號),顯示生產線編號,生產線名稱,班次,生產對象,采用的物料等信息
6.3:膠盆數據查詢:掃描膠盆條碼,顯示該膠盆存放的產品信息,生產線及生產信息,采用的物料信息等;
7.1:通過D/C、卡通箱號段、Wrin Number,查詢裝配數據;
由該裝配數據展開查詢:
7.1.1:查詢該裝配數據由哪幾個外購件批次號組成,以及相應批次的供應商,供應時間,供應數量等信息;
7.1.2:查詢該裝配數據經過幾道工序生產;
7.1.3:查詢該裝配數據由哪幾個批次的膠料組成,以及相應批次的供應商,供應時間,供應數量等信息;
7.1.3:查詢該裝配數據由哪幾個批次的油漆組成,以及相應批次的供應商,供應時間,供應數量等信息;
7.2:通過物料批次號追蹤生產數量;
7.2.1:查詢該物料批次號經過哪幾次生產,分別為哪幾條產線編號;
7.2.2:查詢該物料批次號經過哪幾次噴油,噴油為哪幾個批次號;
7.2.3:查詢廖物料批次號經過哪幾次組裝,組裝后的D/C,卡通箱號段,Wrin Number分別是多少;
7.3:通過工序查詢;
7.3.1:啤機工序查詢:通過該啤機產線編號,日期,查詢當天生產了哪幾個批次的的膠件;
7.3.2:噴油工序查詢:通過噴油產線編號,日期,查詢當天對哪幾個批次的膠件進行噴油,用了哪幾個批次的油漆;
7.3.3:組裝工序查詢:通過組裝產線編號,日期,查詢當天組裝了哪幾個批次的啤件,噴油件,外購件,組裝后的D/C,卡通箱號段,Wrin Number等信息;